Crane structure refers to the main beam, end beam, trolley frame, walk platform, platform, ladder, railings, and conductor frame.
Materials, Parts and Complete Machine Anti-corrosion Treatment
Our company's steel are procured from Anyang Iron and Steel, Handan Iron and Steel and other large steel factory, the material is for the Q235B flat. We can provide the material book and the certificate to the user.
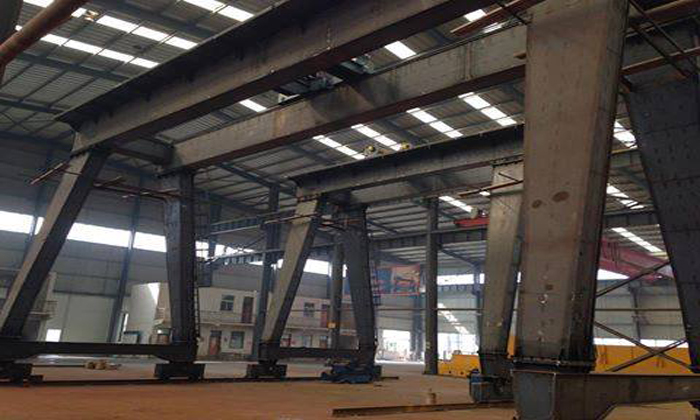
After enter into the plant and the sampling by the laboratory for chemical composition and mechanical properties analysis, unqualified raw materials are not allowed to adopt. Raw material corrosion rating shall not exceed the C-level, all sheet metal must be pre-processed before cutting, parts and complete machine is for shot blasting and manual sandblasting, after that, parts and machine can improve the surface finish and roughness, enhance the adhesion of the primer and substrate, improve the paint film protection and corrosion protection performance, effectively eliminating the product stress in the manufacturing process, improve product quality.
Pretreatment of steel plate need to meet the requirements of grade rust Sa2.5, roughness RZ40-80 mm, WS-type inorganic zinc silicate shop primer 15-20 mm, less than 6 mm of the plate pickling treatment, spray ring Oxygen-rich zinc primer, to prevent the corrosion in the crane manufacturing process.
Crane Metal Structure Flat Orthopedic
Pretreated plate is corrected in the flat-panel machine, to reduce the wave of the web and the cover plate, to ensure the strength of the plate, to reduce the beam under the deflection deformation in the process of using.
Crane Metal Structure Bridge Processing
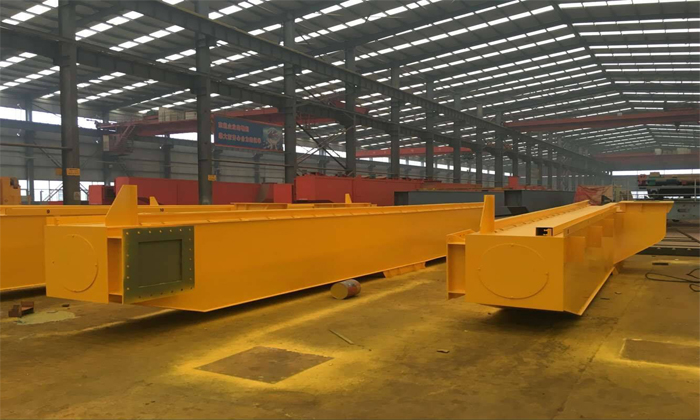
- Steel shot blasting pretreatment to improve the mechanical properties of steel and paint adhesion.
- According to the crane span, the computer control cutting machine, cut out the secondary curve, the fourth curve or two curves of the superposition of the web and the upper plate, so that the degree of pre-crown coincides with crane arch degree.
- With the welding equipment for the main beam welding, welding order according to reasonable arrangements to reduce welding distortion.
- The butt welds of the webs and the upper and lower cover plates use submerged arc welding. The longitudinal welds of the main girder and the end girders are controlled by a computer controlled CO2 gas automatic welding. After welding, 100% of the welds are inspected by X-rays.
- Bridge docking with a large flip machine so that all welding is the flat welding, in order to ensure the welding quality.
- After welding is completed, processing vibration effect in order to eliminate welding stress.
Crane Metal Structure Quality control points
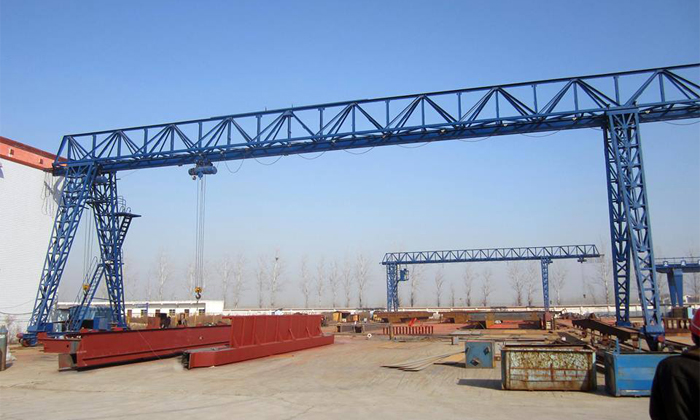
A. Web and upper and lower cover butt weld quality control
- Place each plate on the platform and press firmly with the platen screws to perform the tack welding.
- On both welding sides of the 30 mm degreasing rust.
- Welding direction point to the side of the walk platform by using submerged arc welding machine, according to process requirements to adjust the voltage and current, then records.
B. On the crown control
- Using computer-controlled automatic cutting machine for web cutting, arch curve function F (X) = in (1 -4x2 / s2).
- After the main beam welding, with steel wire, heavy hammer, steel ruler to detect, according to the test results to determine the four weld sequence.
- After the completion of the welding, processing a test on the degree of the arch, if not meet the requirements, using the flame correction method to be amended; if meet the requirements,
- The bridge installation according to a single girder arch value and standard requirements, the use of rail pressure plate in the welding support different locations. Meet the requirements, directly installation.
- After the completion of the bridge, the test by national standards for testing methods, apparatus, in the absence of sunshine, meet the requirements into the loading process.
C. The main beam span control
- The span of the main beam is carried out when the bridge is mounted and the cart is assembled.
- When the bridge is installed, the longitudinal centerline is drawn on the top beam of the end beam, and the cross centerline assembled with the main beam, and the vertical plane of the bending plate is led to the intersection of the upper cover plate and its longitudinal centerline, then drill eye, the main beam and end beam cross center line alignment.
- Adjust the end beam to ensure the required size, in which the span of control based on the nominal size according to the span increase the number in order to eliminate the impact of welding shrinkage. After welding, one end of the steel tape is fixed, put 15 KG tension on the other end of the steel tape and measure the upper plate punching holes and curved plate holes, qualified and transferred into the cart loaded.
- After the cart is installed, measure the span of the wheel in the same way. If there is any problem, adjust the wheel until the technical standard is reached.
Welcome to visit Dongqi Crane factory and you can check the crane metal structure manufacturing process on site.